Production Planning And Control
- Home
- Production Planning And…
Production Planning And Controlling
Production planning and control (PPC) is a must-have for manufacturing facilities that want to stay ahead of the competition. Manufacturers can use these tactics to create a production plan, carry it out, and eventually take control of their operations through continuous improvement programs.
The process of planning and then controlling all aspects of manufacturing and production is known as production planning and control. That includes ordering materials, staffing, machine labor, and even distributing goods to end customers.
A solid production planning and control strategy are essential for any production company’s success. That is because practically all activities within the manufacturing plant are dependent on one another or appropriate production planning and control.
For example, if you had planned to start production on a project at some time but didn’t have the appropriate materials, you’ll have to postpone it. That may involve modifying your manufacturing schedule to avoid equipment idle while you wait for your ingredients. That could lead to late customer orders, particularly if you adopt a just-in-time manufacturing method.
As you can see, production planning and management is a critical component for every manufacturing company trying to optimize operational efficiency and profit margins. We’ll look at some of the most crucial functions and elements of production planning and control in this blog.
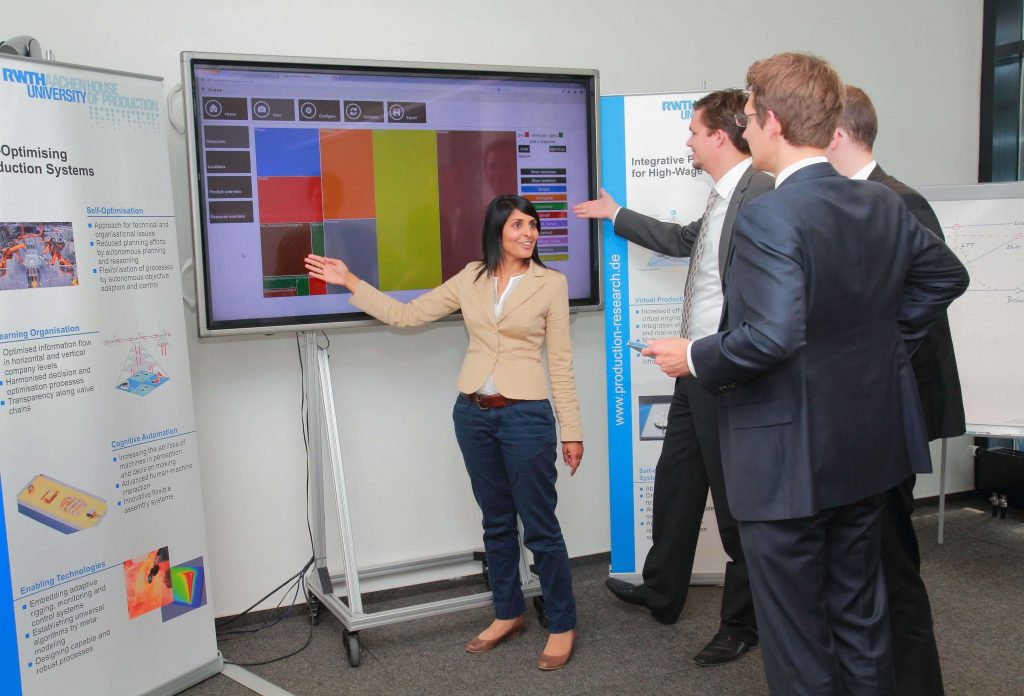
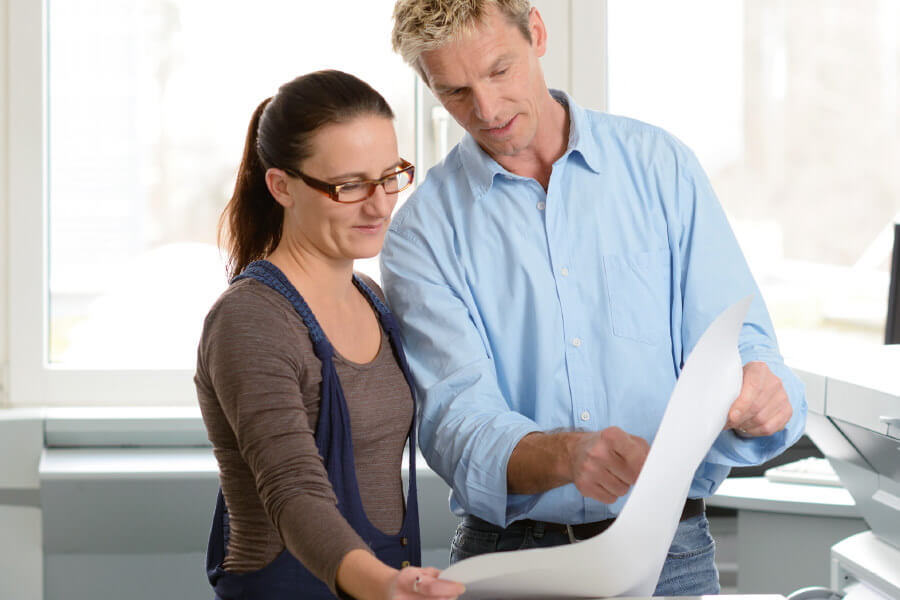
Production Planning
- To ensure right quantity and quality of raw material, equipment, etc. are available during times of production.
- To ensure capacity utilization is in tune with forecast demand at all the time.
- Organization can deliver a product in a timely and regular manner
- Supplier are informed will in advance for the requirement of raw materials.
- It reduces investment in inventory.
- It reduces overall production cost by driving in efficiency.
Production Control
- Regulate inventory management
- Organize the production schedules
- Optimum utilization of resources and production process
- Ensure a smooth flow of all production processes
- Ensure production cost savings thereby improving the bottom line
- Control wastage of resources
- It maintains standard of quality through the production life cycle.
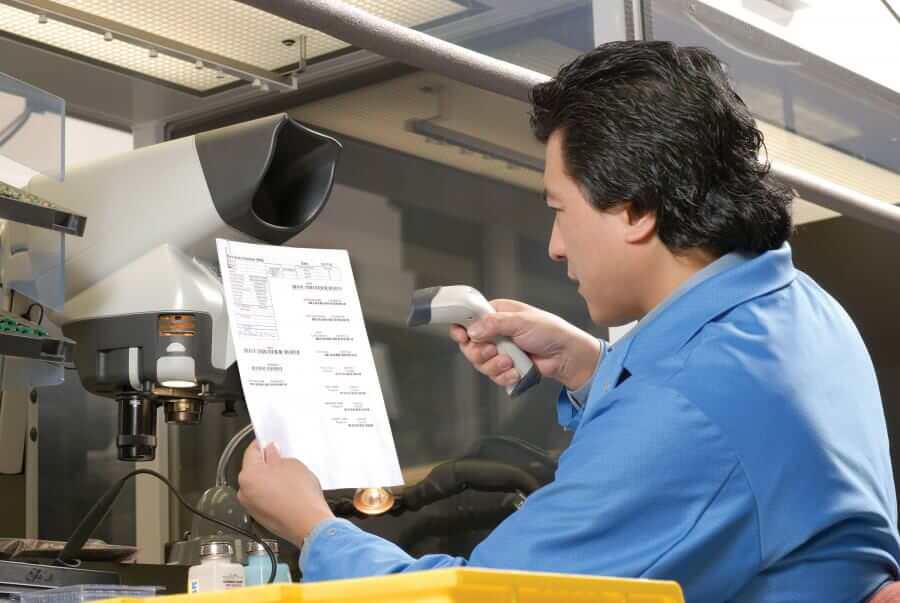
Production Planning & Control Key Functions
The following are some of the most crucial functions in production planning and control:
- Management of Materials
- The precise measurement of materials required for production within a given period is one of the functions of production planning and control. To avoid waste, excessive inventory levels, and other inventory carrying costs, accurately predicting the amount of stuff you’ll need is critical. On the other side, this eliminates the possibility of stockouts and material shortages. Overall, material management allows production to run smoothly since raw materials, parts, and other components can get delivered at a low cost and on schedule.
- Equipment
- The proper operation of equipment gets ensured through production planning and management. That involves looking at equipment downtime to see any bottlenecks or inefficiencies in the manufacturing process. As a result, manufacturing will run smoothly, remain efficient, and will get delivered on time. That component also looks at equipment maintenance schedules to avoid unforeseen malfunctions that would cause production to get halted for an extended period.
- Methods
- The investigation of viable alternatives to production processes, as well as various production schedules, is part of this component of production planning and control. Multiple schedules can be generated by production planning and scheduling software, allowing firms to choose the optimal one for their production processes and restrictions.
- Routing
- Production planning and control, like the previous point, ensure that raw materials get converted into final goods via the most efficient method. This component’s primary goal is to eliminate unnecessary steps or excessive motion around the shop floor.
- Estimating
- Operation timeframes get then estimated after the procedure sheet for operations is made accessible. The function got carried out by analyzing many aspects of operations, such as routing, raw materials.
- Dispatching
- The implementation of the production schedule is part of the control phase of production planning. It entails handing over materials, components, and tools to machine operators for production to begin. As one might expect, this is the point at which the importance of production planning and control gets emphasized. Production will get hampered if there are any delays in obtaining materials or inefficient routes or processes.
- Expediting
- This step is also known as Follow-Up, and it entails monitoring the production process. It also helps material management, work in progress, and assembly. Manufacturers should identify bottlenecks in the manufacturing process and seek to eliminate them in this step to guarantee that the production plan gets carried out as intended.
- Evaluation
- The process, or any process in general, is one of the most critical processes in production planning and control. This section aids in the identification of areas where productivity is still weak and where improvements can get made. Managers can then concentrate on these areas, determining what needs to change and implementing ways to enhance them.
As customer demand for more product variety, faster delivery, and lower cost pressures grow, the software has become a prerequisite for production operations. These technologies allow planners to save time while also being more flexible in altering priorities, production schedules, and inventory plans as they change. Systems can get readily linked with ERP/MRP software to fill in the gaps where these systems lack flexibility, precision, and efficiency in planning and scheduling.
You can use the software to:
- Create optimized schedules that strike a balance between production efficiency and on-time delivery.
- Increase revenue by increasing throughput on bottleneck resources.
- Reduce inventories by synchronizing supply and demand.
- Provide a centralized view of resource capacity across the organization.
- Make scenario-based decision-making possible.
By utilizing the operational data already stored in your ERP system, the Software will propel your manufacturing processes to the next level of production efficiency. The software is a positive step towards increased efficiency and lean manufacturing operations.
Let’s get started
Are you ready for a better, more productive business?
Stop worrying about technology problems. Focus on your business.
Let us provide the support you deserve.
ACT TODAY FOR BETTER TOMORROW
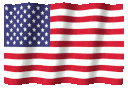
United States
- CorporateServe Solutions, Inc.
- 8 The Green, Ste R, Dover, Delaware 19901, USA
- sales@corporateserve.com
- +1(251)910-8815
- +1(302)572-4685
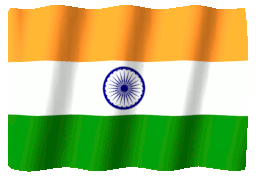
INDIA
- CorporateServe Solutions Pvt. Ltd.
- 408, Udyog Vihar, Phase-IV, Gurgaon,Haryana-122015, INDIA
- sales@corporateserve.com
- +91-9818099176
- +91-9871247733
- +91-9899102817
- +91-124-406 3583
- +91-124-406 6716